Automotive Industry Process Improvement Projects
Productivity Solutions has been improving productivity in the automotive industry for over 20 years. We have been helping tier 1, 2 and 3 automotive suppliers improve their stamping, welding, forming, machining and assembling processes over the past 20 years. Through this, our experience with bending, stamping, welding, machining, assembling and inspecting automotive processes minimizes the time to identify low-hanging fruit opportunities.
Engine Assembly Productivity Improvement
- Workstation engineer on a multi-million-dollar new engine launch team.
- Responsible for ensuring that each of the new 30 manual workstations adhered to Ford's 54 Workstation Readiness criteria categorized under Safety, Ergonomics, Error Proofing, IT – Systems, Process – Standardized Work, Tooling & Equipment & Material Flow for Automotive Industry Services. Subsequently, Created manual workstation layouts and visual aids for training.
- Simulated and designed the staffing model, who when and where, 13 additional operators / shift were required for processing different engine models Automotive Industry Services.
- Power train engineer that reduced labor by loading material line-side instead of in a kit, with line balancing using MODAPTs and workstation layouts. Furthermore, gathered, consolidated, and reported daily quality matrices to management.
Body Stamping & Robotic Welding Facilities – Automotive Industry Process Improvement
- Performed cycle time improvement analysis on highly automated robotic welding cells. Subsequently, prepared several material handling bid specifications for capital expenditure justifications and provided process improvement recommendations.
- Assisted in preparing their 1997 North American Stamping Business Plan and presentation, which identified the capital improvements and associated benefits for the next 5 years.
- Processed several appropriation requests.
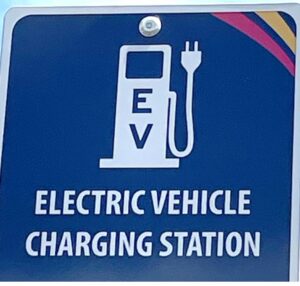
Automotive Body Stamping & Robotic Welding Facilities
- Performed cycle time improvement analysis on highly automated robotic welding cells. Subsequently, prepared several material handling bid specifications for capital expenditure justifications and provided process improvement recommendations.
- Assisted in preparing their 1997 North American Stamping Business Plan and presentation, which identified the capital improvements and associated benefits for the next 5 years. Consequently, processed several appropriation requests.
Tier 1: Blanking, Slitting and Coil Distribution Center
- Performed a due diligence assessment of the facility capacity, storage requirements, operating costs, and manning allocation for a lending institution prior to the requested $80 million construction.
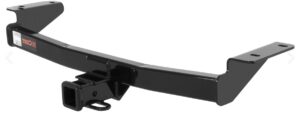
Tier 1: Stamping, Robotic Welding & E-Coating Company
Automotive Tier 1 stamping, welding and coating manufacturer.
- Reduced labor and material handling costs by implementing a Kanban and kitting system to replenish the welding facility from the stamping facility. Consequently, this required several facility layouts, inventory analysis, training, and material handling equipment selection.
- Designed, trained and implemented a labor reporting procedure at the Stamping facility to identify and track process improvements.
- Subsequently, created a companywide capacity model for 15 presses, 24 welding cells, an E-coat paint line and 13 inspection labeling stations for Northern's corporate company to distinguish open capacity for bidding on new jobs.
Automotive Cold Box & Engine Head Casting Facility
Automotive engine casting facility.
- Identified material handling deficiencies of a $6 million automated sand-casting staging equipment prior to implementation.
Engine Assembly Repackaging / Kitting Operation
Automotive engine assembly facility
- Created part repackaging cells to feed assembly workstations.
- And, additionally, Workstation design with material flow racks layouts.